Jay Taylor's notes
back to listing index....Getting Into More Trouble.... | ServeTheHome Forums
[web search]
Original source (forums.servethehome.com)
Tags:
hardware
storage
servers
supermicro
BPN-NVMe3-116UN
nvme
servethehome
sth
forums.servethehome.com
Clipped on: 2023-01-04
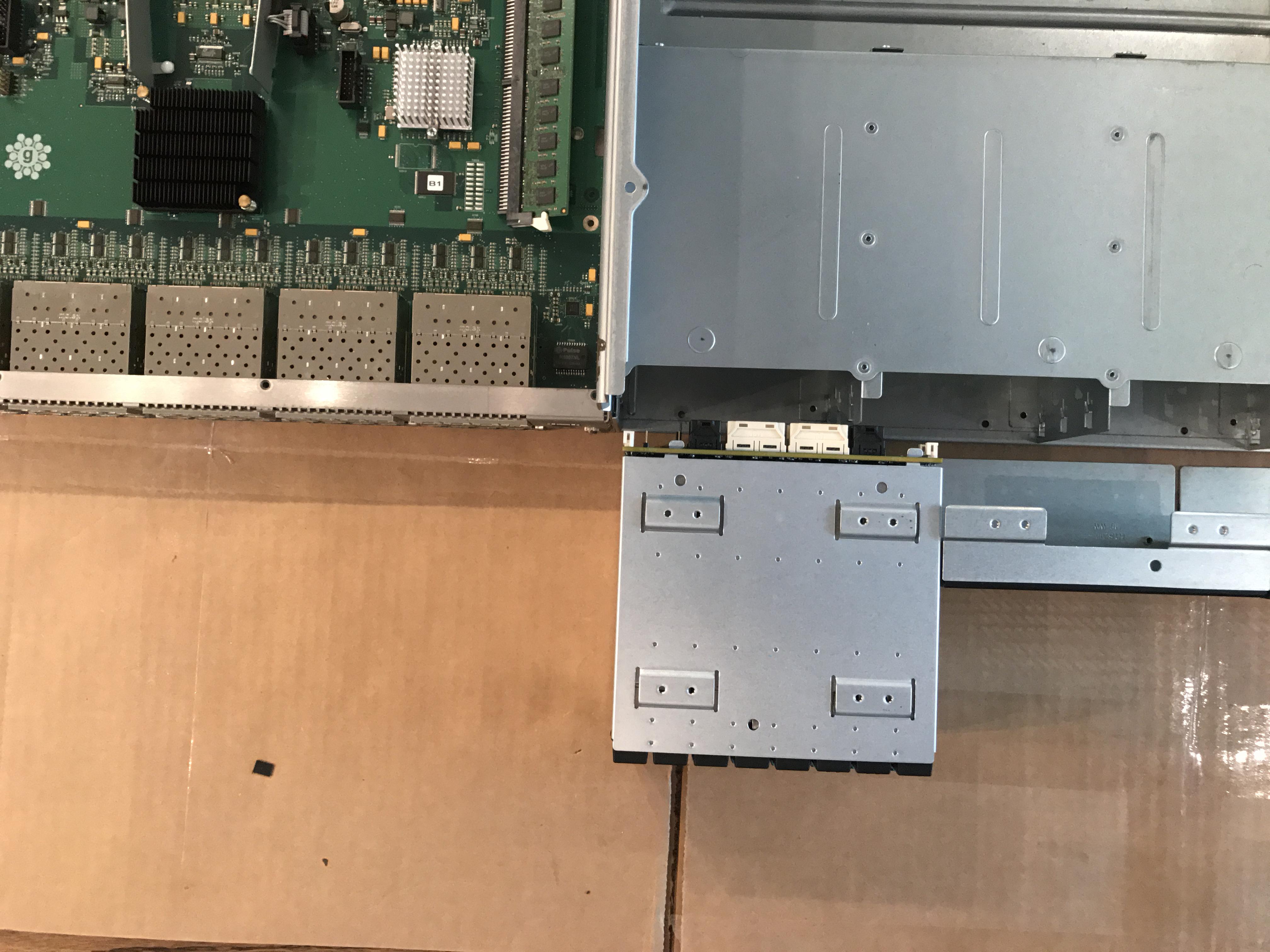
Before you guys start hammering on me:
1. I know they use a proprietary form factor
2. I've seen Supermicro's disclaimer:
"Due to the complexity of integration, this product is sold as completely assembled systems only (with minimum 2 CPU, 4 DIMM and 6 NVMe). Please contact your Supermicro sales rep for special requirements."
3. I recognize that whatever it is I'm doing probably doesn't require 24x+ NVMe drives...
4. etc. etc. etc.....
That being said, SM's high end NVMe storage solutions appear to accomplish this using the following method/components:
For 24x NVMe:
-1x BPN-SAS3-826TQ-B2B (obtainable): "2-port 2U SAS3 12Gbps backplane, support up to 2x 2.5-inch SAS3/SATA3 HDD/SSD"
-1x BPN-NVME3-216EB (No Source Found): "BPN-NVMe3-216A-S4 Backplane Base Board"
-1x AOC-2UR6N4-i4XT-P (obtainable): "2U Ultra Riser with 4-port 10GbE RJ45 (10GBase-T)"
http://www.supermicro.com/a_images/products/Accessories/AOC-2UR6N4-i4XT.jpg
-2x BPN-NVME3-216EL (No Source Found): "PCIe Gen3x16 input to PLX9765 to support 12x NVMe port" ...Although this simply looks like an NVMe expander similar to what you'd see on a BPN-SAS3-216EL1, but for NVMe
-4x CBL-SAST-0819 (Obtainable): "OCuLink v.91,INT,PCIe NVMe SSD, 65CM,34AWG"
-4x CBL-SAST-0820 (Obtainable): "OCuLink v.91,INT,PCIe NVMe SSD, 85CM,34AWG"
-1x RSC-U2N4-6 (Obtainable ~$80 new): "2U Ultra Riser Card with 4 NVME and PCI-Ex16,RoHS/REACH"
-1x RSC-R1UW-E8R (Obtainable ~$40 new): "RSC-R1UW-E8R-O-P"
....They also make this 1u ultra riser which supports 6x oculink NVMe ports (AOC-URN6-i2XT)...

As well as this AOC which includes 4x oculink, plx, and is both cheap and available (AOC-SLG3-4E4T):
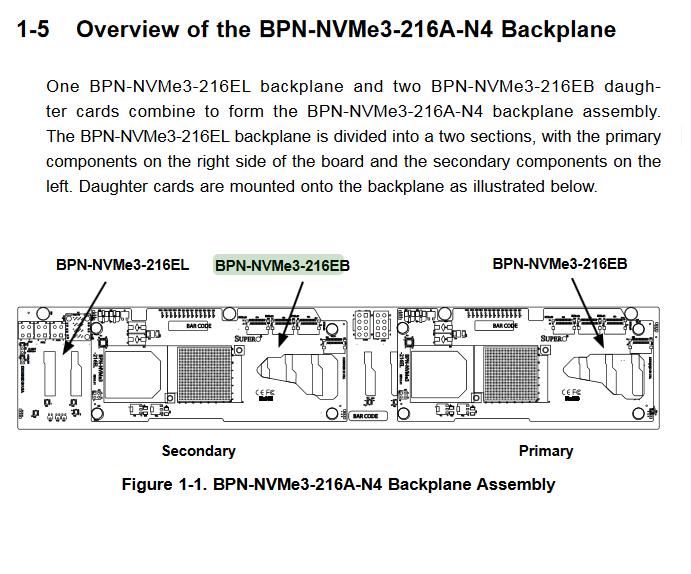
And this AOC w/2x oculink.. even cheaper and available (AOC-SLG3-2E4T):
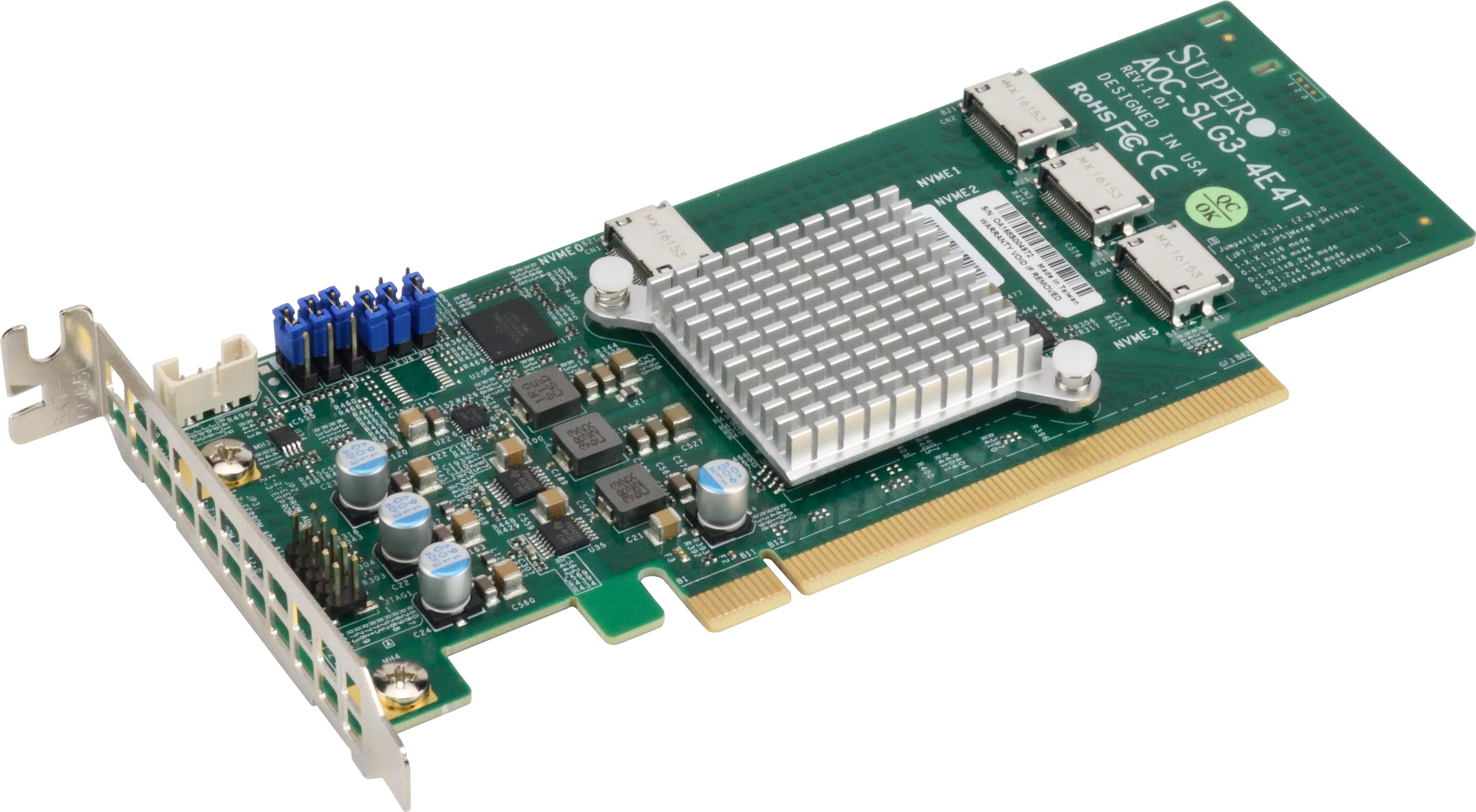
Regarding the 1x BPN-NVME3-216EB and 2x BPN-NVME3-216EL: There are several commonly available SuperMicro 2.5" combo back planes available which support both SAS3 and some quantity of NVMe (e.g. the BPN-SAS3-216A-N4 2U). This is a similar approach to what Intel seems to currently offer, but in a less modular approach..
Then I stumbled across the following user's manual for the (BPN-NVMe3-216A-N4 2U):
https://www.supermicro.com/manuals/other/BPN-NVMe3-216A-N4.pdf
The nomenclature for the other combo back planes usually specifies the number of NVMe slots using the "-N*" at the end of the PN which threw me off a bit in this case...
An interesting excerpt from the manual:

1x BPN-SAS3-826TQ-B2B
1x BPN-NVME3-216EB
2x BPN-NVME3-216EL
Whereas the user manual suggests that 1x BPN-NVME3-216EB + 2x BPN-NVME3-216EL = 1x BPN-NVMe3-216A-N4...
Could it be that, because the BPN-SAS3-826TQ-B2B is simply a TQ pass through, it's just being relabeled/re-purposed in combination with the BPN-NVME3-216EB & BPN-NVME3-216EL cards? If so, I see the BPN-SAS3-826TQ's steeply increasing in value.. This might also lead one to believe that the 216EB and 216EL cards (or possibly the 9400-16i/3840a) might work in combination with other SAS3 TQ backplanes...
May have to start an initiative to corner the 2nd had TQ market!

I guess we'll find out here pretty quickly.
Last edited: May 11, 2017
@Patrick I almost wonder how close a fit it would be for another Intel chassis... the s2600WT2 and the X10DRU-i+ are extremely close in external dimensions...
Listed dimensions are:
Intel: 16.7" x 17"
SM: 17" x 16.8"
I was extremely impressed by the build quality of the Intel unit.
Also really been giving some serious consideration to the possibility of pulling the 2U backplane out of my SC847 and transplanting the GS7200 internals into the lower 2U section under the motherboard tray. This would allow me to both save space and provide serious cfm through the switch chip heat sink.
If attempting that, it wouldn't take a whole lot of extra time to cut and tig weld in the appropriate mounting for converting from one 4U backplane to two rows of 2U backplanes... top all NVME, bottom SAS 3.
Really need time to
Listed dimensions are:
Intel: 16.7" x 17"
SM: 17" x 16.8"
I was extremely impressed by the build quality of the Intel unit.
Also really been giving some serious consideration to the possibility of pulling the 2U backplane out of my SC847 and transplanting the GS7200 internals into the lower 2U section under the motherboard tray. This would allow me to both save space and provide serious cfm through the switch chip heat sink.
If attempting that, it wouldn't take a whole lot of extra time to cut and tig weld in the appropriate mounting for converting from one 4U backplane to two rows of 2U backplanes... top all NVME, bottom SAS 3.
Really need time to
That being said, one of our pipeline certified welders can literally cut a soda can in half and weld it bad together using TIG.
This would obviously be on a bare chassis (which is just metal) and would be more to get the caddy recepticle configuration right when moving from 4 rows of horizontal 3.5" trays to two rows of vertical 2.5" trays.
We weld on machines that have highly complex $100k+ PLC systems implemented all of the time. There are simply precautions that must be taken. No big deal
Last edited: May 10, 2017
Either way please post the build
When you start deploying 4, 6, 8 + chassis in your local rack (or coLo) the big problem with custom stuff is replacement, repair, and general ability to service. It's not there, and now you have to be doing it all... you can't call up and get a replacement part because it's integrated custom, you can't call the DC and have them replace a backplane because it's custom/integrated differently, etc...
With the qty of parts and scale you can/will accomplish with what you're getting/got I think this is something that's going to come back and bite you if you go too far down the 'custom' rabbit hole
Don't let me tell you not to do it someway... search my username I've got/done some crazy ideas too!! Now, years after starting it's amazing how I would have done things differently, and the process going that route now/over time
I've learned that what makes a good, reliable and easily serviceable system usually means not DIYing it unless you have hours/days to spend making it like 'new'.
(While a lot of this is true for at home this is more geared toward businesses. DIYing at home usually isn't time sensitive, etc...)
When you start deploying 4, 6, 8 + chassis in your local rack (or coLo) the big problem with custom stuff is replacement, repair, and general ability to service. It's not there, and now you have to be doing it all... you can't call up and get a replacement part because it's integrated custom, you can't call the DC and have them replace a backplane because it's custom/integrated differently, etc...
With the qty of parts and scale you can/will accomplish with what you're getting/got I think this is something that's going to come back and bite you if you go too far down the 'custom' rabbit hole
Don't let me tell you not to do it someway... search my username I've got/done some crazy ideas too!! Now, years after starting it's amazing how I would have done things differently, and the process going that route now/over time
I've learned that what makes a good, reliable and easily serviceable system usually means not DIYing it unless you have hours/days to spend making it like 'new'.
(While a lot of this is true for at home this is more geared toward businesses. DIYing at home usually isn't time sensitive, etc...)
Jeez.... just rain on my parade why don't you?
We'd have to take some measurements and work it up in cad, but there is a chance it could be integrated quite nicely... basically turning the SC847 into a disk shelf and switch rack.
Remember on the 847 the back half is two 2U layers... the top layer is a sliding shelf that holds the motherboard, and the bottom 2U area is basically a dead space with molex power cables running across it to the 2U backplane.
If that backplane is removed, you basically have a second layer which could easily house a second motherboard (or switch main board). It seems to me that a custom slide out tray integrated into the bottom 2U space (basically a duplicate of the top layer) wouldn't be out of the question. Half of the length in the Gnodal switch is air... it could get a lot shorter.
I think what you'd end up with is something similar to a blade/2 node stacked system. The switch ports would all remain external on the back of the chassis.
Originally this was just a fleeting idea. But now that you guys have turned it into a challenge I think I'll go measure it.